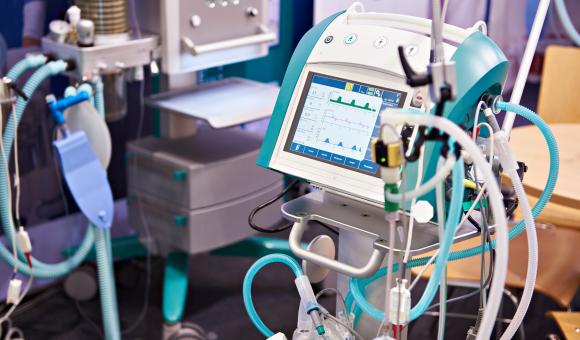
André Bertin, CEO of Namur-based company Coexpair, has taken the lead in resistance to Covid-19. After contacting a doctor friend, he realised that the main technical problem in this battle was replacing faulty parts in respirators, which are essential for patient survival. André Bertin then launched his UFMM (Urgent Fab Med Mat) project and brought with him Safran Aero Boosters, Sonaca and FN Herstal. Among others.
The media have recently featured several articles about companies offering their help to fight Covid-19. And, perhaps surprisingly, it is the CEO of a Walloon aeronautics company who has significantly contributed to launching the movement: André Bertin, from Coexpair.
It was originally a personal relationship, as it often is. The CEO knew a doctor at the CHC in Liège. They worked in the brand new MontLégia building above the city, and the engineer asked the doctor what he could do to help.
The greatest problem posed by the coronavirus is obviously the huge need for respirators, which have been under severe strain in these troubled times, and whose parts have to be regularly replaced. This is where Coexpair can make itself useful.
André Bertin was quick to launch the UFMM (Urgent Fab Med Mat) project, and established two main risks. The first involves shortages of PPE (personal protective equipment) items, mainly masks, to be precise, but also overalls and the consumables for ventilation machines, respirators. The second risk involves the machines themselves: respirator parts and syringe pumps, the small infusion pumps for injecting small quantities of fluid into a patient.
The replacement of respirator parts was the first urgent priority. Some of these parts only require a tiny adaptation, such as the tubes. Others require tests and calibration, but this is not particularly difficult (filters, etc.). Yet others require more advanced technical modifications, such as the flow sensors or valves. There were a number of possible different processes for the manufacture of these parts, such as moulding, machining or 3D printing. Syringe pumps are a special case, as Coexpair can try to adapt its own miniature syringe.
But André Bertin is looking further ahead… He wants to develop his own respirator. Due to the emergency, this machine would have simplified features but, faced with an (almost) blank page, the CEO wanted to think out of the box. For example, why not immediately consider a respirator for several patients? Particularly as prototypes exist, that have been developed by universities - UCLouvain in particular - and laboratories. Furthermore, André Bertin uses industry specific management tools, such as those for aeronautics projects, shared websites and digital tools.
However, André Bertin is aware that Coexpair will not be enough, as it needs support from large groups.
This message was immediately heard by François Lepot, CEO of Safran Aero Boosters. André Bertin told the Herstal-based giant which respirator parts may soon become a problem. The Safran teams set to work in the next few hours. As this newsletter was being finished - as everything is moving very quickly at the moment - prototypes for the flowmeter, a part that wears out particularly quickly and could soon become unavailable from international suppliers, will be produced by 3D technology using four different plastics. The goal is to be ready for production in around ten days, at the beginning of April.
An important detail: Safran Aero Boosters will not charge the hospitals anything, as it considers its action to be a community gesture.
FN Herstal, a neighbour and distant cousin of Safran Aero Boosters, had already worked directly with Liège hospitals, including CHC; it also joined the initiative led by André Bertin, with an attitude of solidarity and to facilitate the coordination of efforts. The proposal by FN Herstal involved providing its technical capabilities in the 3D printing of metal and polymers for the manufacture of respirator parts. At the start of the venture, the Liège company organised itself to start studying and producing the parts in question.
Lastly, Sonaca also became involved, immediately making its purchasing and supply chain expertise available to better identify and schedule the critical supplies of consumables such as filters.
But let’s get back to UCLouvain... While André Bertin was starting to plan, the Louvain university was heading in the same direction, but via a different route, with its Openhub. Another Walloon aerospace company, Aerospacelab, is also involved. Its CEO, Benoît Deper, stressed the “wonderful interaction” between universities and businesses. And the Breath4Life respirator is on track and should be available within a week. This machine was created to meet an urgent need, not for commercial purposes.
In accordance with André Bertin’s wishes, the project has come full circle... The two projects have come together beautifully and, as this article is being completed, there are 141 active members working on the respirator project. There will be more by the time you read this...